1 Feb, 2024 | sheila | No Comments
electrical motor controls for integrated systems 5th edition pdf free
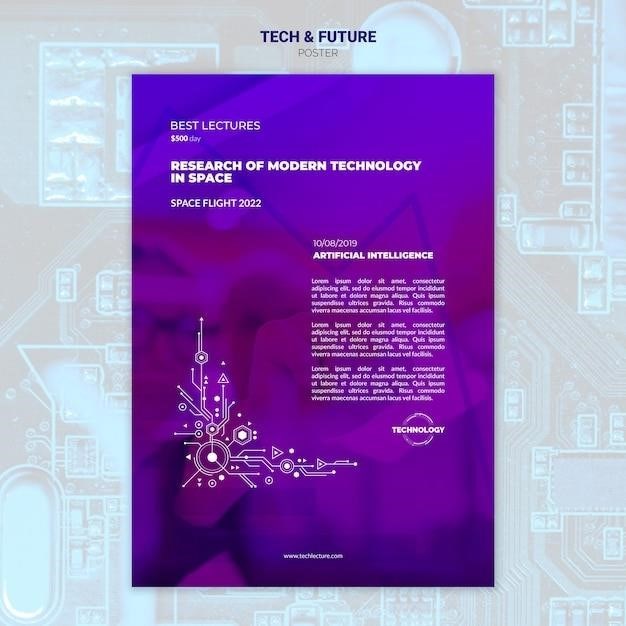
Electrical Motor Controls for Integrated Systems⁚ A Comprehensive Guide
This guide explores the essential aspects of electrical motor controls‚ focusing on their application within integrated systems. It delves into the key components of these systems‚ including motor starters‚ motor drives‚ programmable logic controllers (PLCs)‚ semiconductors‚ and control devices. The guide also provides troubleshooting procedures and examines the diverse applications of electrical motor controls across various industries. Finally‚ it discusses future trends shaping the field of electrical motor controls.
Introduction to Electrical Motor Controls
Electrical motor controls are the brain and nervous system of modern industrial machinery‚ orchestrating the precise movements and operations of automated systems. They act as the intermediary between human commands and the physical actions of electric motors‚ ensuring smooth‚ efficient‚ and safe operation. Understanding electrical motor controls is crucial for anyone involved in industrial automation‚ manufacturing‚ or any field that utilizes electric motors for power and motion.
These control systems encompass a wide array of components‚ each playing a critical role in regulating the motor’s speed‚ torque‚ direction‚ and overall performance. This intricate network of components‚ including motor starters‚ motor drives‚ programmable logic controllers (PLCs)‚ semiconductors‚ and control devices‚ works in concert to execute precise motor commands and adapt to changing conditions.
The evolution of electrical motor controls has been driven by the relentless pursuit of greater efficiency‚ precision‚ and safety in industrial automation. Advancements in semiconductor technology‚ digital control systems‚ and software development have led to increasingly sophisticated and adaptable motor control systems. These systems are now capable of seamlessly integrating with other industrial components‚ creating a comprehensive and interconnected network for optimal performance.
The Importance of Electrical Motor Controls in Integrated Systems
In today’s interconnected industrial landscape‚ electrical motor controls play a pivotal role in the seamless operation of integrated systems. They act as the linchpin‚ enabling complex machinery to function in harmony and achieve optimal performance. These controls are not merely passive regulators; they are intelligent coordinators‚ adapting to changing conditions and optimizing motor operation for maximum efficiency and productivity.
The significance of electrical motor controls in integrated systems extends beyond individual motors. They are the bridge that connects various components‚ ensuring that each element works in concert with others. This interconnectedness allows for the automation of complex processes‚ streamlining production‚ minimizing downtime‚ and enhancing overall system reliability.
Furthermore‚ electrical motor controls are essential for achieving safety in integrated systems. They monitor motor performance‚ detecting potential issues like overheating or overload‚ and implementing corrective actions to prevent catastrophic failures. This proactive approach to safety is crucial in high-risk industrial environments‚ where malfunctioning motors could pose serious hazards.
Key Components of Electrical Motor Control Systems
Electrical motor control systems are comprised of various interconnected components‚ each contributing to the overall functionality and efficiency of the system. These components work in tandem to control‚ protect‚ and optimize the operation of electric motors‚ ensuring smooth and reliable performance. Key components include⁚
Motor Starters⁚ These devices provide the initial power surge required to initiate motor operation. They can be simple contactors for basic applications or more complex starters incorporating overload protection and other safety features for demanding industrial environments;
Motor Drives⁚ Motor drives are electronic devices that control the speed‚ torque‚ and direction of electric motors. They provide precise control over motor operation‚ allowing for tailored performance in various applications. Modern drives often utilize advanced technologies such as variable frequency drives (VFDs) for energy efficiency and precise speed control.
Motor Starters
Motor starters are essential components in electrical motor control systems‚ serving as the initial power source that brings motors to life. Their role is to connect the motor to the power supply‚ providing the necessary current to overcome inertia and initiate rotation. While seemingly simple‚ motor starters play a crucial role in ensuring safe and efficient motor operation.
There are different types of motor starters‚ each designed for specific applications and requirements. Simple contactors‚ for instance‚ provide basic on/off control‚ while more complex starters incorporate features like overload protection‚ undervoltage protection‚ and thermal protection. These safety measures are vital in preventing motor damage due to excessive current‚ voltage fluctuations‚ or overheating.
The selection of a suitable motor starter depends on factors such as the motor size‚ operating environment‚ and the specific control requirements of the application. In industrial settings‚ where motors often operate under demanding conditions‚ robust and reliable starters are crucial for ensuring uninterrupted production and minimizing downtime.
Motor Drives
Motor drives represent the heart of sophisticated electrical motor control systems‚ offering precise control over the speed‚ torque‚ and direction of rotation. Unlike traditional motor starters that simply provide power‚ motor drives act as intelligent controllers‚ allowing for fine-tuning of motor performance according to specific application demands.
The advanced capabilities of motor drives stem from their integration of power electronics‚ microprocessors‚ and sophisticated control algorithms. These drives can adjust motor speed seamlessly‚ responding to changing load conditions or external commands. This adaptability is crucial in applications requiring precise control‚ such as robotics‚ automated assembly lines‚ and material handling systems.
Beyond speed control‚ motor drives offer a range of features that enhance efficiency and optimize motor operation. They can implement energy-saving strategies by reducing power consumption during low-load periods‚ and they often incorporate built-in diagnostics for early detection of motor faults‚ minimizing downtime and maintenance costs.
Programmable Logic Controllers (PLCs)
Programmable Logic Controllers (PLCs) serve as the brains of modern industrial automation systems‚ providing the intelligence and decision-making capabilities that orchestrate complex processes. These robust and versatile devices are designed to handle a wide range of tasks‚ including controlling motor drives‚ monitoring sensors‚ and managing data flow within an integrated system.
PLCs are essentially specialized computers that have been hardened to withstand the harsh environments common in industrial settings. They feature a modular design‚ allowing for easy expansion and customization to accommodate specific application needs. This flexibility makes PLCs ideal for both simple and complex automation tasks.
A key strength of PLCs lies in their ability to execute user-defined programs‚ typically written in a ladder logic language‚ which resembles the wiring diagrams of traditional relay-based control systems. These programs define the logic of the automation system‚ dictating how the PLC responds to inputs from sensors and actuators‚ and how it interacts with other components within the integrated system.
Semiconductors
Semiconductors are the foundation of modern electronics‚ including those used in electrical motor controls. These materials‚ with their unique ability to conduct electricity under certain conditions‚ form the basis of transistors‚ diodes‚ integrated circuits (ICs)‚ and other essential components that power the intricate workings of motor control systems.
In the realm of motor controls‚ semiconductors play a crucial role in power electronics‚ enabling the efficient conversion and control of electrical power. Transistors‚ for instance‚ act as high-speed switches‚ allowing for precise control of current flow within motor circuits. Diodes‚ on the other hand‚ ensure unidirectional current flow‚ preventing reverse current that could damage sensitive components.
Integrated circuits (ICs)‚ also known as microchips‚ are complex semiconductor devices that combine multiple transistors‚ diodes‚ and other components on a single chip. These highly integrated circuits form the core of motor drives‚ allowing for sophisticated control algorithms and advanced features‚ such as variable frequency drives (VFDs)‚ which provide precise control over motor speed and torque.
Control Devices
Control devices form the interface between human operators and the intricate workings of electrical motor control systems. They act as the command center‚ allowing for manual and automated adjustments to motor operation‚ ensuring safety‚ and providing vital feedback on system performance.
Push buttons‚ switches‚ and selector switches are common control devices‚ providing manual control over motor start‚ stop‚ direction‚ and speed. These devices allow operators to directly interact with the system‚ initiating specific actions or modifying settings as needed.
Beyond manual control‚ control devices encompass a range of automated elements‚ such as limit switches‚ proximity sensors‚ and pressure sensors. These devices monitor specific conditions‚ such as motor position‚ proximity to objects‚ or pressure levels‚ triggering actions or alarms based on pre-determined thresholds. This automated feedback mechanism ensures safe and efficient operation‚ preventing potential damage and optimizing system performance.
Troubleshooting Procedures for Electrical Motor Controls
Troubleshooting electrical motor controls is an essential skill for technicians and engineers working with integrated systems. It involves a systematic approach to identify and resolve issues that may arise‚ ensuring the smooth and reliable operation of the system.
The process typically begins with a thorough visual inspection‚ checking for loose connections‚ damaged wiring‚ or signs of overheating. Understanding the system’s schematic diagram is crucial‚ allowing for tracing the flow of electricity and pinpointing potential fault locations.
Testing with multimeters and other diagnostic tools is vital for measuring voltage‚ current‚ and resistance‚ providing valuable insights into the system’s behavior. This data helps to determine whether the problem lies in the control circuitry‚ the motor itself‚ or other components within the system.
Troubleshooting often involves a combination of careful observation‚ logical deduction‚ and systematic testing. By following a structured approach and utilizing the appropriate tools‚ technicians can effectively identify and resolve issues‚ ensuring the continued functionality and reliability of the electrical motor control system.
Applications of Electrical Motor Controls in Various Industries
Electrical motor controls find wide-ranging applications across numerous industries‚ playing a crucial role in automating processes and enhancing efficiency. Their versatility allows them to control a diverse range of motors‚ from small‚ precise servomotors used in robotics to large‚ powerful motors driving heavy machinery in manufacturing.
In manufacturing‚ electrical motor controls are integral to assembly lines‚ conveyor systems‚ and machine tools‚ ensuring precise movements and consistent production. In the automotive industry‚ they control electric vehicles‚ hybrid systems‚ and automated assembly processes‚ contributing to advancements in fuel efficiency and vehicle performance.
Beyond these sectors‚ electrical motor controls are employed in building automation systems‚ HVAC systems‚ and water treatment facilities‚ optimizing energy consumption and enhancing comfort. Their applications extend to agriculture‚ where they power irrigation systems and automated farming equipment‚ and to transportation‚ where they control electric trains and other forms of mass transit.
The wide-ranging applications of electrical motor controls demonstrate their vital role in modern industrial processes‚ contributing to increased efficiency‚ productivity‚ and safety across diverse industries.
Future Trends in Electrical Motor Controls
The field of electrical motor controls is constantly evolving‚ driven by advancements in technology and the growing demand for increased efficiency‚ energy savings‚ and automation. Several key trends are shaping the future of this field‚ including the integration of artificial intelligence (AI) and machine learning (ML)‚ the development of more sophisticated control algorithms‚ and the adoption of advanced power electronics.
AI and ML are poised to revolutionize electrical motor controls‚ enabling predictive maintenance‚ real-time optimization‚ and adaptive control strategies. These technologies can analyze data from motor sensors‚ predict potential failures‚ and optimize motor performance based on real-time conditions‚ further enhancing efficiency and reliability.
Advancements in power electronics‚ such as the development of high-power‚ high-frequency switching devices‚ are leading to smaller‚ lighter‚ and more efficient motor drives. These advancements will enable the development of more compact and energy-efficient motor control systems‚ suitable for a wider range of applications.
As these trends continue to unfold‚ the future of electrical motor controls holds immense potential for innovation‚ driving advancements in automation‚ energy efficiency‚ and industrial productivity.
Write Reviews
Leave a Comment
No Comments & Reviews